Sigma Q&A, late summer 2022: I series lenses, Foveon update, and why the new 16-28 mm f/2.8 is so good
posted Saturday, November 5, 2022 at 6:16 PM EDT
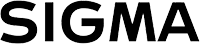
This is the final article about the series of interviews I had with photo-industry leaders on my last trip to Japan in July of 2022, and I've saved the best for last :-)
SIGMA's Kazuto Yamaki is my favorite interview subject because of his unique position and unusual candor. As the CEO of SIGMA, he doesn't have to worry about someone higher up the corporate chain coming down on him for saying the wrong thing in an interview, so he can be more open than most. He's also unique among top industry executives in how closely he works with the engineers who actually design and build SIGMA's products. He respects and elevates his engineering staff more than any other executive I've met, and I think this is a key factor in the quality and value of SIGMA's products.
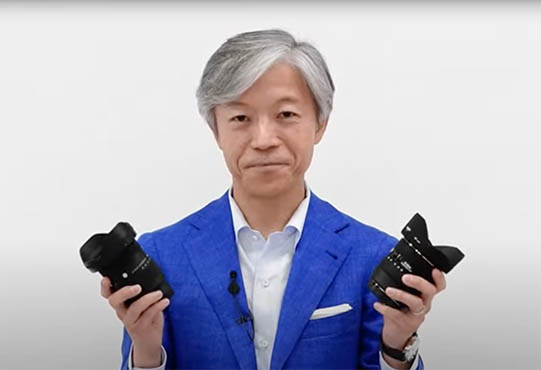
Yamaki-san's close involvement with both the engineering and manufacturing staffs means that he can answer virtually any question about the company's operation, from high-level strategy to technical details of how their lenses and cameras are designed and produced. I had an hour-long rambling conversation with him covering a wide range of topics, read on for all the details!
Other interviews and articles in this series:
- Tour of the new SIGMA headquarters
- Pansonic interview
- Fujifilm interview
- OM Digital Systems interview
-
Sony interview
How did COVID impact your supply chain and production?
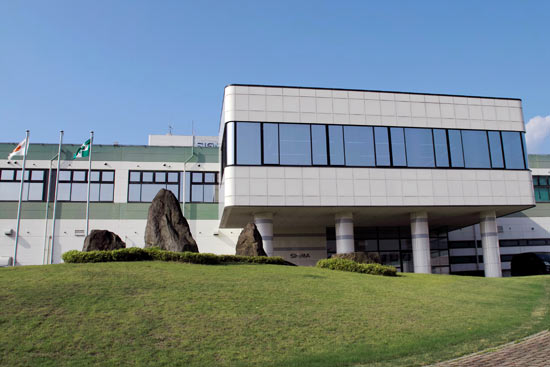
RDE: The COVID-caused supply chain issues have been a challenge for almost everyone in the industry. SIGMA is in a unique position, though, with your factory located in Japan and a lot of your suppliers here also. Have you still had supply-chain issues? How did COVID affect production within your own factory?
KY: COVID affected our production system of course, but the magnitude of the impact to our production system has been much smaller compared to other companies. That’s the reason why we could provide products quite smoothly, with the usual timing, during the very severe time of COVID in 2020 and 2021.
RDE: So from the customers’ and dealers’ standpoints, they didn’t really notice a disruption?
KY: Yeah, I think so. In 2020, the demand, especially from the American market, was very high because the government subsidized the public and also stimulated the market, so we did have some supply shortage problems, but it wasn’t because of a production problem, but rather very high demand.
RDE: Ah, too much demand, that’s interesting. So the US stimulus worked very well for stimulating SIGMA, then. <chuckles>
KY: Very well, yes. We had some issues, we had some problems getting parts from suppliers, but I think that compared to big companies we had a much smaller problem. First of all because we have a smaller supply chain, because we have just one location in Japan, and most of the parts suppliers who machine parts and do sub-assembly for us are located very close to our factory as well. I think over 50% of our suppliers are in the Fukushima prefecture, and if you include the surrounding prefectures like Yamagata, Miyagi and generally the northeast Tohoku area, more than 80% of our suppliers are located in that region. And the rest of our suppliers are in the Nagano prefecture, which is also well-known as a source for high-precision small parts suppliers. So we don’t source parts from overseas…
RDE: So actually, all of your supply chain is in Japan?
KY: Except for raw materials and semiconductors. So for those two types of parts or materials, we had problems like other companies. But for small parts and components, we had relatively fewer problems.
RDE: Do you think your more-stable production capability helped you gain market share over the last two years?
KY: In some countries yes, especially in the US, China and Europe we could gain market share. It wasn’t huge, but yeah, we did gain some.
RDE: Yeah, it’s not like all of a sudden you doubled your market share, but it was a noticeable increment.
KY: Of course, we can’t actually double our production capacity. We make everything by ourselves so we can’t increase the capacity by that much, but we did increase our share.
What do you project for the next 12-24 months?
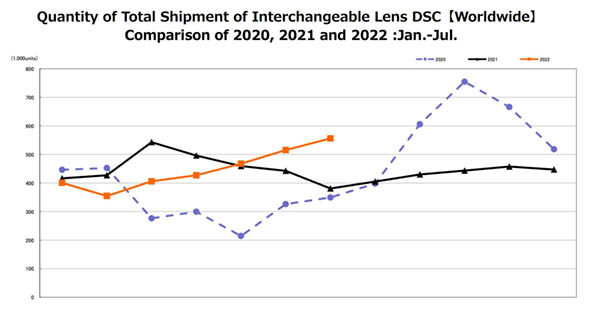
[This was recorded at the end of July, 2022, so is based on Yamaki-san’s sense of the market at that time]
RDE: It’s hard to say where we are with COVID. Just as it seemed that things were getting better globally China went into widespread hard lockdowns. Now most of the world and especially the US is seeing high inflation. What are you projecting for the industry as a whole and your business in particular over the next 12-24 months?
KY: That’s a very tough question! It’s very difficult to predict, but I think the US market will be a bit slower than last year, because last year was so good, and now the market is suffering from high inflation and also the reaction from last year.
RDE: Ah, you mean that so many people purchased lenses last year that now those people don’t need more lenses?
KY: Yes, that’s true for the US, but it seems that the other markets in Europe and Asia seem to be quite stable.
RDE: Interesting; Europe and Asia didn’t see the surge you saw in the US, because they didn’t have such aggressive stimulus programs, but they’re continuing to be stable.
KY: Yes.
RDE: So the overall level of business, if you take out the US surge caused by the government stimulus checks, when you compare it to pre-COVID, has it been fairly stable, or has it gone up some? I mean just in general, around the world…
KY: In general, compared to pre-COVID, for SIGMA, I think it’s quite stable, or slightly positive. So I think it’s OK. But if we have new mounts, our business might be even better.
What’s the impact of the current exchange rates?
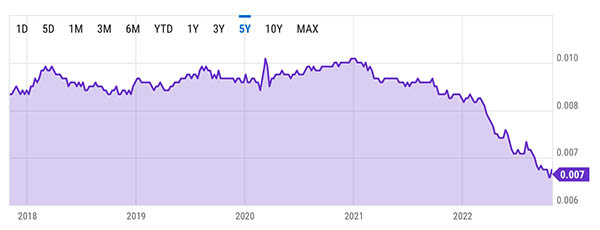
RDE: That’s great, it sounds like things are going really well for you. Another part of this is the current exchange rates. We’ve talked about this before; with all of your production in Japan, the value of the Yen has a big impact. When the Yen is weak, that of course means that you have better profits. Are there any other factors? I don’t really know what to ask about, but are there any other effects of the weaker Yen that someone on the outside might not realize?
A little explanation: With their factory in Japan, SIGMA’s manufacturing costs are in Japanese Yen, but their sales in other countries are in those countries’ local currency. When the Yen is weak, foreign sales bring in more money relative to their production costs, so SIGMA’s profits are better. Conversely, when the Yen is strong, their production costs are that much higher relative to their international revenue. Yamaki-san had explained this to me in the past, but I was curious if there were factors that might act in the other direction, hence my question here.
KY: A weak Yen can affect our costs for raw materials and some parts. In most cases, we purchase the raw materials from outside Japan, in US dollars. So those suppliers ask us to increase their prices. Almost every week, we received a request to increase the price, for several months. So our procurement costs are much higher than before. But when it comes to interchangeable lenses, the manufacturing costs are the dominant factor, rather than the raw materials.
RDE: Ah, I see: A weaker Yen isn’t entirely positive, because you have to source the raw materials, but they’re not that large a part of the overall cost.
Most of us tend to think of the glass in lenses as “just glass”, but it’s actually a very sophisticated product in its own right, with a wide range of possible characteristics. It’s a very highly-engineered material, and its price reflects that. So just the optical glass alone is a significant cost item for lens makers.
(For a peek at the incredible manufacturing process for optical glass, check out this article about my tour of Nikon’s Hikari glass factory in Akita, Japan. It's a fascinating process!)
Some questions and background on the I series lenses
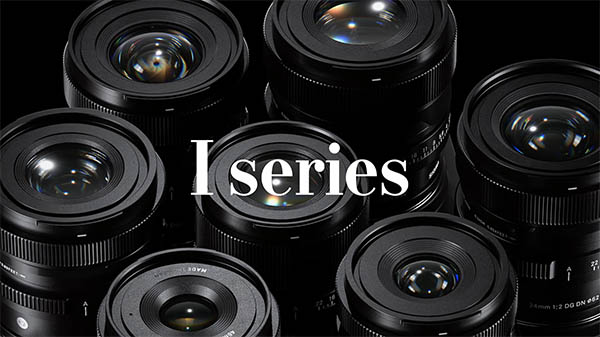
RDE: You announced the I series of prime lenses last October, and you now have no less than seven of them. I’m very interested in this lineup, in their positioning within the market, their designs and their construction. First off, what led to their development? The first thing mentioned on your product page for the line is the photographer’s experience when using them, how they feel in the hand, how they feel to use. Did that focus on the experience of using them come from any particular customer feedback, or was it more something that you just recognized internally at SIGMA, that people like things that feel nice? How did that whole line start?
KY: There were mainly two reasons. First, we wanted to have that kind of lens. Here in SIGMA there are many people who love camera lenses, photography and imaging. So they wanted to have that kind of lens; compact, small, not super lightweight but still lightweight, but with a high-quality feel overall.
RDE: Yeah, it’s kind of a classic feel, a bit like the way an old manual-focus lens feels in your hands.
KY: Right, yes. We realized that this isn't mainstream in the market today, but we believe that it’s SIGMA’s mission to offer such a unique product in the market. There are many f/2 or f/1.8 compact lightweight prime lenses, and their prices are quite affordable, but also their feel is a little bit cheap. So such lenses are already available from other manufacturers, but a lot of them are offering a similar type of product, and we wanted to offer something unique. That was our first reason.
The second reason is that we wanted to offer good lenses for our fp camera. Because lightweight and high-quality feel lenses are a good match for the fp camera.
RDE: They’re a good pairing with the fp, for sure. Personally, they feel very well-positioned to me, they’re the kind of lenses that I’d enjoy myself. I don’t buy so many lenses any more, but the I series are for the pure enthusiasts, the people who really love the process of photography, that’s who they connect with. I think there are a lot of those people out there too.
KY: I personally like them. Today, I personally only use I series lenses.
RDE: Hah, that says a lot, because you could have literally any lens you want :-)
Is the I series all-metal construction important to their excellent feel?
RDE: When I first learned about them, I was surprised to see that they’re all-metal, rather than using the TSC (thermally stable composite) plastic that’s worked so well in so many of your lenses to date. Does using metal vs TSC make a big difference in the handling, or is it part of producing a lens that people will recognize as “high build quality” if you say it’s all-metal?
KY: Hmm, TSC functionally is great, but still it’s not as good as aluminum when it comes to operational feel. We wanted to give the lenses a better operational feel.
RDE: Depending on production volume, I’d expect the per-unit manufacturing cost of a lens with machined metal parts vs TSC molded ones to be higher. Obviously, if it’s a short run, making the high-precision molds for TSC is very expensive, but if it’s a long run, the cost of machining the metal for each lens would be higher.
KY: Much higher.
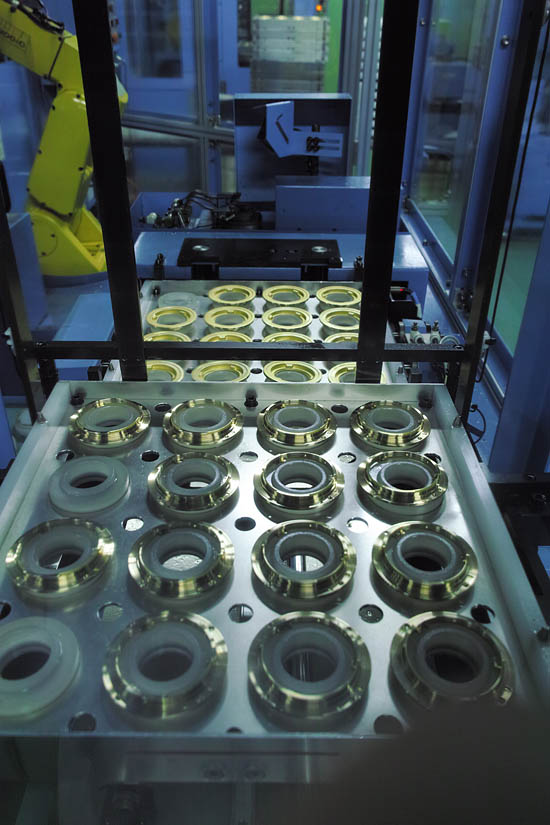
RDE: Much higher, yeah. The decision to go all-metal was all about the feel in the hand and how it would feel to the user. Have there been advances and/or cost reductions in CNC machines that make metal parts less expensive than they were in the past, though?
KY: It helps. But having said that, the production costs for metal parts are much higher than plastic parts. But we introduced several automated CNC machines that provide better precision at lower cost. - I mean shorter cycle times, but still the cost is higher.
High-speed CNC machines aren’t cheap, so they’re major investments. Combined with the time it takes to machine parts vs simply molding them, this means that metal parts are significantly more expensive than plastic ones. Given that, I’m surprised that SIGMA is able to sell the I series lenses at what I consider to be very affordable prices for such high-quality prime lenses. They’re far from cheap, but $650 or $750 still strikes me as pretty affordable given the build quality and optical performance.
How much did new technology help in making the I series lenses possible?
RDE: The I series lenses are all remarkably compact for their combinations of focal length and aperture. They still use a fair amount of aspheric and SLD/FLD elements, but not as many as their f/1.4 Art predecessors. While they’re a full stop slower than the f/1.4 Art models, I’m still surprised that the designers could achieve such compactness with generally much simpler optical formulae and yet still achieve MTF curves nearly as good as some of the Art models. What do you think the factors were that allowed the designers to accomplish this? Have there been continued advances in your aspheric molding technology? Have new glass formulations contributed? Are there any other factors?
KY: Yes. It’s not just one solution that helped accomplish this design, there are multiple factors that contribute. First there’s new aspherical element technology; we are continuously developing that kind of technology. Second, we are getting more and more newer glass materials, mostly high refractive index glasses.
RDE: Ah, right, higher refractive index glass makes it easier to make very compact lenses.
(Refractive index is basically a measure of how much light bends when passing through a lens. A high refractive index means the light can be bent more sharply, so the lens doesn't need to be as big overall to do its job. Recent developments by glass makers have led to new glasses with unusually high refractive indices.)
KY: Right, this is very important. And also we have accumulated a lot of knowledge/technique/know-how, to know how to achieve higher optical performance with fewer optical elements or fewer parts.
RDE: That’s interesting; some of it is just purely gaining experience with the design, that lens designers can come up with different formulations that they didn’t have before.
KY: Yes.
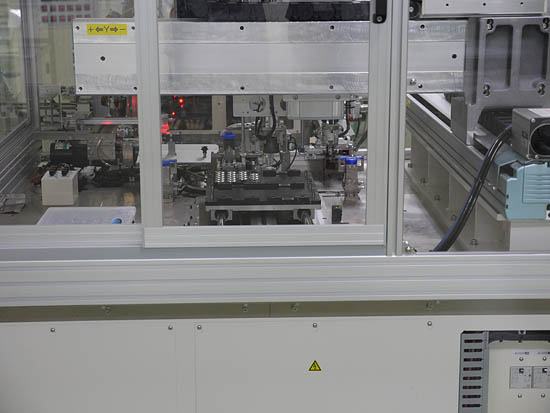
RDE: With the aspheric molding, what are the nature of the advancements there? I know for one thing that it’s very tricky to mold an aspheric element where the thickness varies a lot from the center to the edge. Can you say anything about what sorts of things, what types of advances you’ve made in the aspheric molding technology?
KY: In the past, there were many limitations to being able to mold a specific shape. For example, double-concave, double-sided aspheric lenses were very difficult to make. Or we couldn’t make an extreme aspheric lens that had a huge peak to valley value, because if there’s a thick part and a thin part, it’s very difficult to cool down the elements without distortion.
RDE: Oh right: Even if you could avoid the lens shattering when you cooled it down after molding, there could still be stresses that would distort the image.
KY: Yes. So as we accumulated experience, we have been able to relax such limitations. So now our optical engineers are having more and more options to design the new lenses with.
RDE: So it’s a combination of higher refractive index glass, and also that you have the ability to make more extreme aspheric elements now. As a result, you don’t need as many elements to achieve a given level of optical performance.
KY: Yes.
Is there anything else that contributes to the I series’ affordability?
RDE: I guess it follows from all of the above, but the combination of compact size and excellent optical performance and all-metal construction is surprising to find at such relatively affordable prices. Other than the simpler optical formulas, are there any other factors that contribute to the I series affordability?
KY: I think there are mainly two reasons behind it. First of all, we make the parts that require higher precision ourselves. If we outsourced those, the cost would be very high, because the higher the precision, the higher the cost. So even if we outsourced them from a supplier, if we asked for higher precision, they would charge a lot. So we only outsource the simple parts from suppliers, then make the complicated parts by ourselves. By doing that we can keep the production costs lower. The second reason is that during this period, we also developed the manufacturing technology to get higher yield. Because we make most of the key components ourselves, we can make some adjustments, very sophisticated adjustments during assembly. By combining these two approaches, we can have higher yield compared to previously. In short, we have higher productivity or higher yield; eventually that contributes to keeping the production costs down.
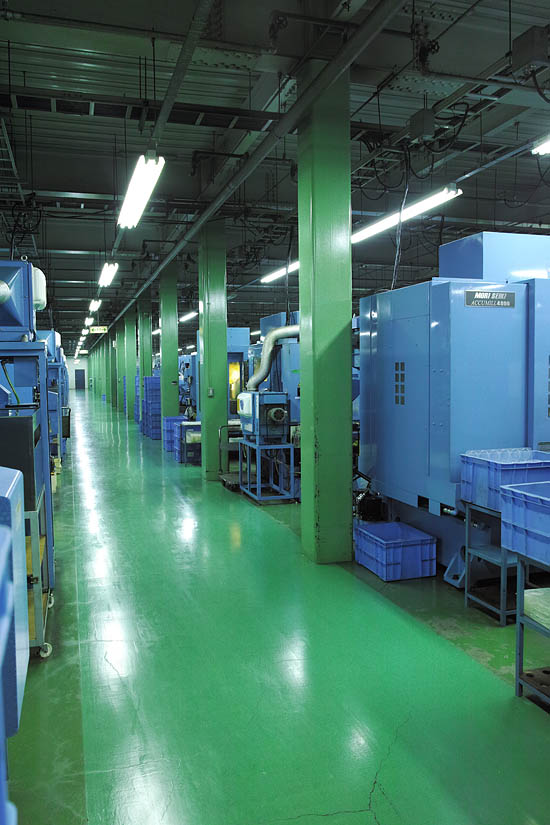
RDE: Ah, that makes a lot of sense. In some ways, your strategy for outsourcing is almost the opposite of what most companies do; I think most companies tend to look for outside suppliers with expertise to handle the most complicated parts.
KY: Yeah. Part of the advantage of having such tight tolerances [in our own internal production] is that our parts are truly interchangeable, which leads to much more efficient production. With lower-precision parts (such as could result from having different vendors providing complex parts), the workers have to find parts that match each other on the production line. Because we make all the very high-precision parts ourselves, our workers don’t have to do that, so our assembly process is more efficient, and it’s easier to maintain very stable optical performance in everyday production.
RDE: Yeah, I see the point. Companies that outsource a lot of high-precision parts lose control of factors that are critical to achieving high yield. I guess they could just tighten the specs with their providers, but then that would make the parts that much more expensive.
KY: Yes.
I found this very interesting: As I said in the conversation, companies often outsource parts needing special handling or processing, but SIGMA does the opposite, at least when it comes to parts with tight tolerances. For an external supplier, the cost of maintaining tight tolerances would cut yield to the extent that they’d have to charge significantly more for the parts than ones having specs more typical of their general output. Internally though, SIGMA’s investment in the needed equipment and (even more importantly) the highly-skilled operators to run it actually reduces their overall costs through more efficient production and higher yields. SIGMA’s production-line workers can just pick up parts and put them together, without having to hunt for sets that happen to work together. I’m not quite sure how to express it, but this seems very characteristic to me of what I’ve seen over the years of SIGMA’s pragmatic approach to manufacturing: There’s a constant focus on optimizing the overall process, rather than just tweaking the individual parts of it, and a logical approach to finding the points of greatest leverage.
What new mounts are coming?
RDE: You’re already supporting an incredible range of mounts: The traditional SLRs from Canon and Nikon, Sony E-mount, L-Mount and Micro Four Thirds. That’s a lot to manage, but you recently announced that there would be “at least one more” mount coming in 2022. Are you ready to say anything about that yet? Does “at least one” mean two? Three? ;-)
YK: The new mount that I mentioned was the FUJIFILM X mount, so we already released that. For the other mounts, we would like to support as many mounts as possible, but today I can’t share any more detail about that.
What does the new L2 alliance between Panasonic and Leica mean for SIGMA?
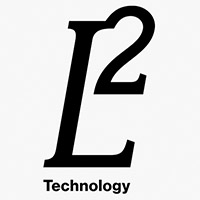
May of 2022.
RDE: What does the new L2 alliance between Panasonic and Leica mean for SIGMA? Will that place you at a disadvantage in competing with them for L-platform lenses?
KY: There is no negative impact to the L-Mount Alliance. We still have regular committee meetings and conferences between the three companies about how we should develop the L-Mount Alliance. In the L-Mount Alliance, the three companies are basically independent in terms of product development and sales, although we may work together jointly on marketing. The L-Mount Alliance means that [we’re] using the same platform, the same L-Mount platform and developing the L-Mount system so the users can have the benefit. But in terms of product development, as I said, each company is independent. Before the L-Mount Alliance, SIGMA was independent and developed our own products by ourselves. And this will continue in the future too. But still, we work together with Panasonic and Leica for the L-Mount Alliance. What I’d like to tell you is that we still continue the conversation about how to develop the L-Mount system that will be beneficial for the users. We always think about the users. So each company can develop their own technology, but the mission of the alliance is to make sure that the L-Mount users won’t have any issues with compatibility between the cameras and the lenses in the L-Mount alliance. Some lenses may not be the best suited for some technology, but we try hard to minimize any such disadvantages.
RDE: So with L-Mount, it sounds like there’s a very strong focus on the user, and the L-Mount Alliance wants an L-Mount lens to be an L-Mount lens regardless of the body it’s being used with, not some different flavor of it that works here but not there. (I will actually be meeting with Panasonic on Friday, so this will be some of my questions for them as well.)
Although I’m publishing this article quite a while after the one covering my interview with Panasonic, I actually met with Panasonic just a few days after I met with Yamaki-san. That article makes interesting reading, to hear Panasonic’s take on the L-Mount Alliance and how the new L2 alliance fits into it. The short version of the story is that there won’t be any negative impact on the L-Mount Alliance, in terms of either compatibility or marketing. Yamane-san of Panasonic told me that Yamaki-san is actually a close personal friend of his, that he had talked with him prior to the contract with Leica, and that they both agreed to work together to improve the L-Mount system. I had had some concern that L2 might lead to lenses having more capability with one company’s cameras vs another, as occurred with Micro Four Thirds. Having spoken with both gentlemen personally, though, I’m happy to say that I now have no concerns whatever in this regard.
The “shockingly good” 16-28mm f/2.8
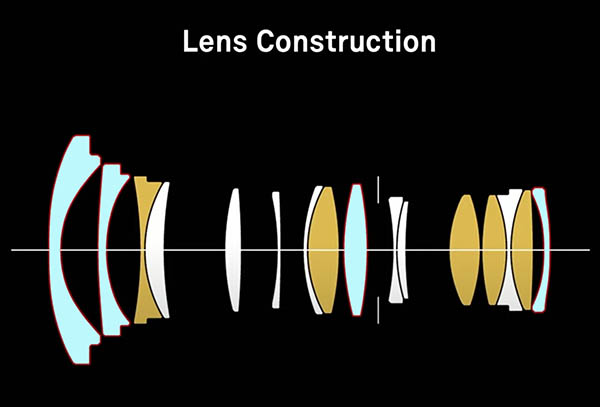
RDE: The new 16-28mm F2.8 DG DN | Contemporary looks like a fantastic lens, I mean some people have called it “shockingly good”. It really seems to be very high-spec in terms of its sharpness and optical performance, especially for the $899 price point. The only complaints I’ve heard from anybody is that it’s not quite as fast autofocusing as some lenses, and that its sunstars are just so-so. (Sunstars seem to have become the latest hot fad :-) [We had a brief side discussion about sunstars, Yamaki-san wasn’t familiar with the term. I’d never heard about it as a thing before either, until I was researching about the 16-28mm F2.8 DG DN | Contemporary prior to this interview. I guess they’re a thing now… :-)] Bottom line though, I’ve heard almost no complaints about the lens at all. I can’t recall where I saw it mentioned, but did you say that you already have an Art version of this lens planned. (Is that correct?) What would an “Art” version bring to the table? Will it be another in your f/2 lineup? Maybe more video-oriented, with even less breathing at the wide end? (The 16-28mm F2.8 DG DN | Contemporary already seems quite good for video, with very little breathing.)
KY: We already have one, that’s our 14-24mm F2.8 DG DN | Art.
RDE: Ah, right - that’s roughly the same focal length range, just slightly wider…
KY: Yes, a wide-angle large-aperture zoom lens … which is also very high performance. Actually, in terms of optical performance, it’s better than the 16-28mm F2.8 DG DN | Contemporary.
RDE: Yeah, and actually, you also have the 18-35mm F1.8 DC HSM | Art zoom lens, that we were just blown away by back when it first came out. I remember seeing our test results from that lens and thinking “Holy mackerel, that’s not like a zoom, it’s like a kit of high-end primes in that range!
KY: Yes, that was for SLRs.
SIGMA has a history of producing amazing wide-angle zoom lenses. I remember how astonished I and the rest of the IR team were way back in 2013 when we first got our hands on a sample of the SIGMA 18-35mm F1.8 DC HSM | Art. It was a very wide-aperture wide-angle zoom lens that at every focal length beat most wide-angle prime lenses on the market. It was like having a bagful of top-notch primes that just happened to be packaged a single lens barrel. That was almost 10 years ago now, and it was a revolution in terms of what people could expect from zoom lenses. SIGMA’s design and manufacturing expertise has only increased since that time, leading to superb lenses like the latest 16-28mm F2.8 DG DN | Contemporary
What’s the status of the new Foveon sensor?
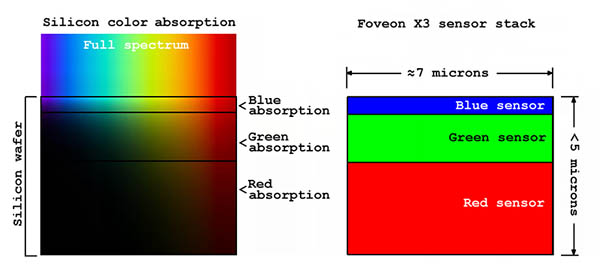
(Image via Wikimedia Commons, CC BY-SA 3.0)
RDE: Of course, there are also questions people have about the development of a full-frame Foveon sensor, which I know has been a very long and difficult process. I think on your site it sounded like the development of that sensor is now based in Japan. Is that true, or do you still have a California operation?
KY: That’s true. This project started several years ago, and at that time, the project was run by our team in California. But it didn’t go well, so I decided to move the main operation to Japan, and now the engineer here is in charge of that project.
RDE: Ah, you have an internal engineer here now that runs it. Is that a new person? I’d think that would take a lot of very specific semiconductor experience. Or does it more just come down to general project management skills?
KY: We’re jointly working with one company…
RDE: Ah, it’s a joint effort with the foundry.
KY: Yes, because we’re not experts in that field, so we need a partner.
RDE: Got it, but the engineering management is now in-house, and up to your standards or expectations. Back in February of this year, you said in a press release that there were three phases to the sensor development process: Design and simulation, test-chip prototyping, and development of a full-frame prototype.
KY: Actually, the first phase is a prototype of pixel structure. The second phase is a prototype of a pixel that has the same size as the final product’s (but the sensor size is smaller).
RDE: Ah yeah, just the pixel first, then a sensor. At the time of that press release, you said that you were in the second phase of the process. Can you say anything about how that’s been going?
KY: Unfortunately, we are still waiting for the prototype. Our partner is now making the prototype. As you know, semiconductor makers are extremely busy right now. So there’s been a little bit of delay.
RDE: Yeah, the whole semiconductor industry, COVID just threw a wrench into all of it. Everybody is having trouble getting chips it seems, so that makes sense.
Checking back with SIGMA prior to posting this article, they told me that they've since received the test chip from the foundry and it’s currently undergoing tests and evaluation.
RDE: It’s been over 6 years since the sd Quattro and sd Quattro H were announced. There’s been enormous increases in image processor speed since then. I’m not sure how to turn this into an intelligent question, but what impact will those kinds of advances in processor capability have on the full-frame Foveon when it finally arrives? Will they allow more sophisticated color-management processing, or will it more just be a matter of running the same algorithms much more quickly?
KY: I think so. Otherwise, we can’t release the new product, it wouldn’t make sense to release a new product with a new sensor. With the new technology, our goal is to achieve both better processing time and a better result.
RDE: Ah, so it’ll impact both factors positively. It’ll affect image quality, color quality and also speed.
I take this as overall positive news for the Foveon sensor. It’s of course disappointing that the full-frame sensor has suffered so many delays, but the positive news is that issues contributing to problems with its development have been addressed. Having a capable engineer managing the project from SIGMA’s headquarters and surrounded by the rest of SIGMA’s engineering team has to be vastly more efficient than a team located an ocean away. I also suspect that the project’s management took a step up in quality and capability in the process. (Yamaki-san is very good at hiring and retaining top engineering talent.) While the current upheaval in the semiconductor industry will be an ongoing challenge, I was left feeling a bit more optimistic about the long-term prospects for Foveon technology.
What are the chances for phase-detect AF in the next Foveon sensor?
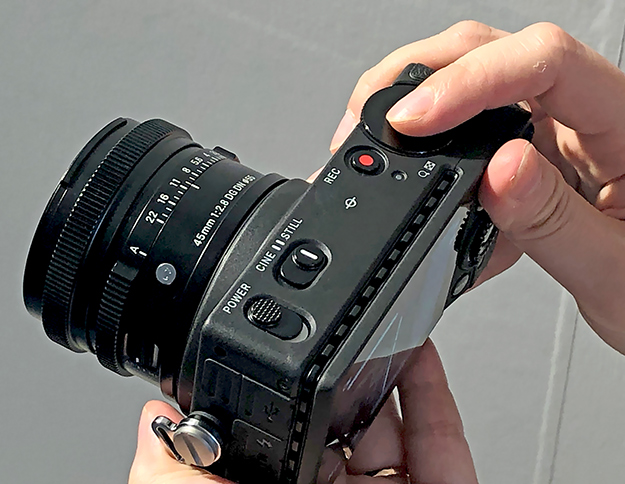
RDE: This may be getting the cart very much before the horse, given that you’re still working on the development of the basic pixel itself, but is there a chance that a full-frame Foveon chip could also incorporate PDAF?
KY: Ah, actually it’s quite early to be able to say anything about that. But as long as I see the market demand, and also in terms of the autofocus performance, the phase detection is the best solution. So I personally believe we need to implement phase detection AF, but we haven’t made a decision.
RDE: Yeah, that was one of the differences between the fp and the fp L. (This actually makes me realize how long it’s been since we last saw each other, because so much has gone on; the fp L was announced a while back, but it was still after I was last here.) It has the same form factor and its basic functions are very similar, but at the same time it’s a very different beast: 61MP vs 24MP, now with PDAF vs CDAF. $2,500 vs $1,700. It looks like it’s aimed at a very different market, is that the case? Is it more stills-oriented, or is it still very much a still/video hybrid. Who are the typical users of the fp L?
KY: The situation is a bit different from country to country. The biggest market for the fp and fp L is still Japan. In the case of the Japanese market, it seems that the majority of the users take still photos. There are some who shoot video, but the majority of the users are still photographers. But when it comes to the US market or Europe, it seems that there are more and more video users, users who shoot more video than stills. So with the introduction of the fp and fp L, we didn’t define the type of target customers clearly, and we said “this camera is for everyone”, whether you take still photos or videos. But that may have confused the market, and people may believe “this is a video camera”, rather than one for still shooting. But still some people realize that this is a good compact camera for still photography. So that confusion may have been felt by potential customers, and affected our business.
RDE: Ah, so each group was maybe thinking that it was a camera for the other group. With the fp L though, its higher resolution does make me think of it more as a still camera. So with that, are … I guess this would primarily be in Japan, because you said the Japanese market is more still-oriented, so is the fp L selling more than the fp in Japan?
KY: When it comes to the price, the fp is still much lower than the fp L, so many users still choose the fp, especially younger ones.
RDE: So based purely on the price, the fp is selling a good bit more.
KY: Yeah.
RDE: The fp L now has an AA filter. (Anti-aliasing or low-pass filter.) Some have said that’s for video, but video resolution would be so much lower that an AA filter designed for video would blur the 61mp stills way too much. I’m kind of curious that the higher-resolution sensor has a low pass filter, whereas the lower-resolution one didn’t. That seems kind of opposite to what I would have expected. What’s that about, how did it end up that the fp didn’t have low-pass, but the fp L does?
KY: If you look at the anti-aliasing, you’re right, the aliasing is more visible with lower resolution than with higher resolution. But if you look at the resolution, using the AA filter on 24 MP would also deteriorate the resolution. So we wanted to prioritize the resolution at the risk of aliasing. But when it comes to the 61MPl, it has lots of resolution. So having a weak AA filter may not affect the image quality.
RDE: Ah yeah, you probably wouldn’t notice a reduction in resolution when you’re starting out with so much to begin with, but the moirés go away.
KY: Yes, so we looked at the picture and then decided whether we should put on the AA filter or not.
What’s the latest with the factory?
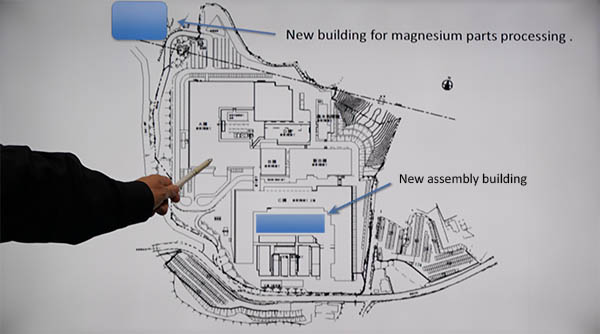
RDE: It’s been quite a while since I last visited your factory. The last time I was there, you had recently constructed a new building with an impressive array of machines specifically for machining magnesium alloy. At the time you were planning to construct another building. Has that now been completed, and what is it used for? Did this expand your overall capacity or was it a matter of adding new capabilities, as with the magnesium machining facility? Have there been other additions?
KY: Actually we built two new buildings. The one is for packaging and warehouse space, as well as repair. It’s a bit outside of the main factory area, maybe three minutes away by car. Within the factory area, the new building is for assembly. As I said, the modern assembly line is getting longer and longer, because during assembly we check all the details of the performance; we adjust the centering adjustment, or during assembly we check the resolution, so we have introduced a lot of measurement instruments, so we needed more space. In short, I can say that we needed a new building for higher quality, because the new assembly lines require lots of checking and adjustment, so that’s why the line keeps getting longer.
RDE: So it didn’t increase throughput… well, maybe it increased yield … but it didn’t increase your overall capacity.
KY: No, it didn’t increase capacity.
RDE: So it’s not like you’re making 20% more lenses now.
KY: Yeah.
RDE: I remember it was a significant improvement or benefit for the line when you implemented the proprietary MTF measuring system, using it so much to check everything.
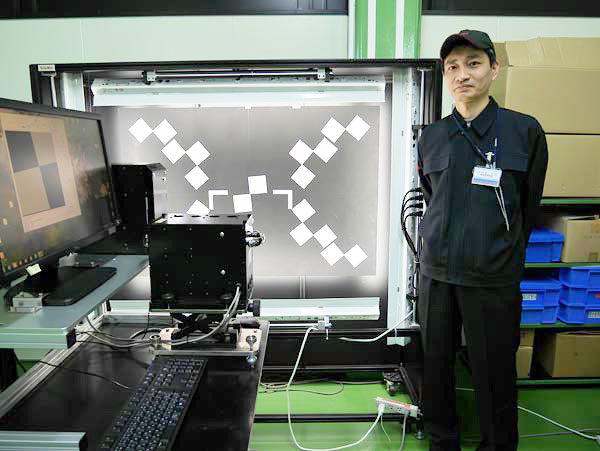
I got an exclusive look at SIGMA’s in-house MTF testing system back in 2015 and you can read about it here. The shot above shows one of the systems and its creator Mr. Masatoshi Ishii. As far as I know, SIGMA was the first (and is still the only?) manufacturer to test 100% of their lenses before shipping them. (This applies to their Global Vision line of lenses, first announced at Photokina in 2012, more than 10 years ago.) As Yamaki-san mentioned above, they’ve also incorporated extensive testing directly into their production lines, ensuring that various sub-assemblies are within the tight tolerances established for them before being assembled into finished lenses. The constant focus on precision and quality throughout the production process results in high manufacturing yields, which are key to SIGMA being able to offer high-quality lenses at affordable prices.
The challenges of being an independent lens manufacturer
RDE: This is just a general curiosity: There’s been such a transition in the industry, it went from SLRs where there were basically four mounts, with three of them accounting for most of the volume, and now it seems like we have so many mounts, with the old ones fading. What’s it been like as a manufacturer, trying to adapt as all these changes came through? It seems like it must have been a very tricky process to manage.
KY: The most challenging part is to have software engineers to monitor the development of the new systems. We try to catch up to the development of the new mounts as much as possible.
RDE: Ah yeah, you basically have to reverse-engineer what the communications are between the lenses and the bodies. So the critical bottleneck is the software engineering to do that. I can imagine that’s quite challenging.
RDE: Well, I think that’s all my questions, we talked for quite a while. It’s always so great interviewing you, because you don’t have to think what someone else higher up the chain is going to say about it. You don’t have to worry about clearing it through four layers of bureaucracy. <both chuckle> Thank you so much!
KY: Thank you
RDE: It’s really great to be here and doing this again.
KY: And I’m very happy to see you again…
Summary
I'm actually not sure how to summarize such a wide-ranging conversation. I think my bottom-line takeway from the meeting is that SIGMA continues very solidly on its course. They continue to grow and expand, having just this year moved into a beautiful new headquarters building (it really is beautiful, check out my photo tour of it), recently expanded their factory and shipping facilities and continue to roll out new products that combine performance, quality and value. Demand for their products is high, and the global monetary balance is currently very much in their favor. They're also a company steeped in photography, both historically and in the present (many of their engineers and Yamaki-san himself are photographers), leading to products like the I series lenses, as well as high-quality, value-priced workhorses like the new 16-28mm F2.8 DG DN | Contemporary. I can't wait to see what they'll have in store the next time I visit, when I'm in Japan for CP+ 2023 in late February of next year; stay tuned for that!
(As usual, I'll try to monitor comments for this article closely for the next little while; feel free to ask any questions about any of the above that I might be able to answer for you!)